How modular building is changing the future for healthcare
- Loom Craft Modular
- May 1, 2020
- 3 min read
Around the world, modular and prefab construction is on the rise, in particular within the healthcare industry. According to a study by McGraw Hill Construction, 49% of all healthcare projects utilise prefabrication1, up from 37% in 2011. So why are such incredible numbers of hospitals, aged care facilities and medical buildings embracing this way of building?
Prefabrication – notably modular prefabrication – comes with many advantages for all sectors, including cost savings, significantly shortened construction schedules and minimised on-site disruption, however this modern method of construction lends itself particularly well to the interests of the healthcare industry.
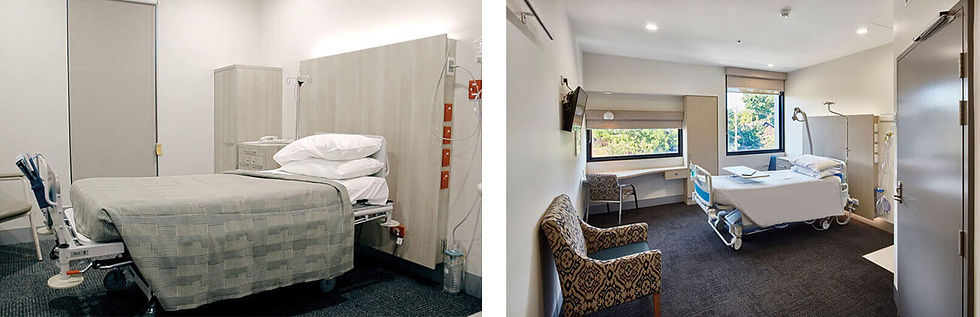
Faster construction times
While traditional builds can take years to complete, modular construction comes with a fixed timeframe and can accelerate project timelines by 20-50%2. The hastening of healthcare build times is advantageous in the most commonplace of scenarios, however in times of emergency response, as is currently being experienced in relation to COVID-19, it can be crucial.
By constructing within a controlled factory environment, weather delays are eliminated, building construction is able to occur simultaneously to on-site works, while multiple stages of a building, and the development of multiple buildings, can occur concurrently.
In addition, engaging with a turn-key prefab builder enables the client a single point of contact for the whole project, streamlining communication and the project as a whole.
For rapid adaptation to changing requirements and getting patients in beds faster, particularly in times of crisis, modular construction provides the healthcare sector with an incomparable advantage.
Minimises disruption
By constructing the project off-site, the majority of the disruption, noise and debris that results from traditional construction is eliminated. This is particularly important for the healthcare industry, where sanitation and comfort are crucial to patient recovery and the resident experience. Research surrounding the impact that the healthcare environment has on healing is widespread, with a 2018 study finding that excessive noise in hospitals “has been implicated in the development of intensive care psychosis, hospitalisation induced stress, increased pain sensitivity, high blood pressure, and poor mental health.” Not only does it have an effect on patients, but also staff by “reducing the intelligibility of speech and impairing communication, causing annoyance, irritation, and fatigue.”
Modular and prefabricated construction drastically minimise that noise. By taking most of the construction off-site, trades are required on site for only days – compared to what can be months with a traditional build – reducing noise, dust and disruption to the day-to-day running of the health facility, improving hospital capacities, and creating a significantly improved environment for both patients and staff.
Cost savings
While a study by McKinsey & Company found that, in the right environment, modular construction can cut costs by 20%, it greatly favours projects that feature a degree of uniform repetition, such as aged care facilities and hospitals. With repetition comes capital cost savings in prefabrication, and effortless duplication for future additions.
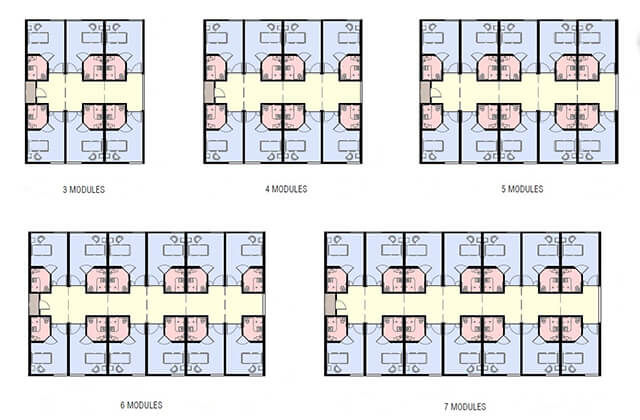
Additionally, costs associated with modular construction are fixed from the get-go. Each project has a high level of documentation, so the design is heavily resolved, while every drop of paint, every nail and every screw is pre-determined, pre-costed and accounted for, leaving no surprises or price blow-outs later in the process.
Meanwhile, for aged care and medical buildings in which rooms generate income, the sped-up process of prefabrication allows the hospital to create that income faster. For example, in some cases, the prefabricated modular solution can be manufactured, delivered and installed in half the time of conventional construction. This creates a significant increase in revenue for the facility and a significant reduction in the cost of funds.
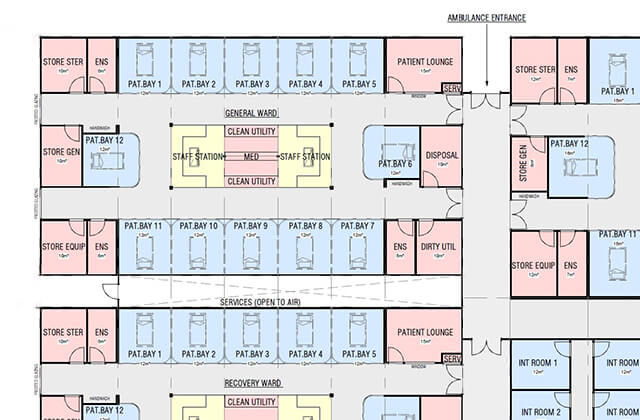
Modular construction allows healthcare clients to not only take advantage of these immediate cost-savings, but also to generate potential cost savings further down the track thanks to the intrinsic future-proofed nature of modular buildings. These structures are fully constructed off-site, craned into place and bolted into the ground using steel footings. The advantage of this is that the modules can be moved to another site at a later date, sold and moved to other facilities if they are no longer required, added to using other modules or disassembled into smaller wards. This makes modular an ideal and cost-effective long-term solution for healthcare spaces where fast and continuous changes in requirements are commonplace.

Comments